By Sean Buckley, Life Sciences Industry Consultant, Emerson
Maintenance Scheduling
Equipment reliability spans several areas—asset performance, line and unit performance, problem detection and visibility, and unplanned downtime avoidance. It takes significant time and effort by a wide variety of maintenance and production personnel to determine when to perform required preventative maintenance (PM) on production equipment. Once planned, the PM can also adversely affect production as planning can’t easily account for real-time changes, resulting in loss in technician productivity and sometimes putting the process at risk if the asset is now needed for production but offline for maintenance.
Using Emerson’s Real-Time Modeling System (RTMS) integrated with plant floor execution systems such as the DeltaV distributed control system and Syncade manufacturing execution system provides real-time updates to scheduling. Since this software always reflects actual production status, the maintenance staff can easily schedule repairs or updates to minimize production impact, ensuring that maintenance does not start to prep for a job that had to be canceled due to production schedule changes.
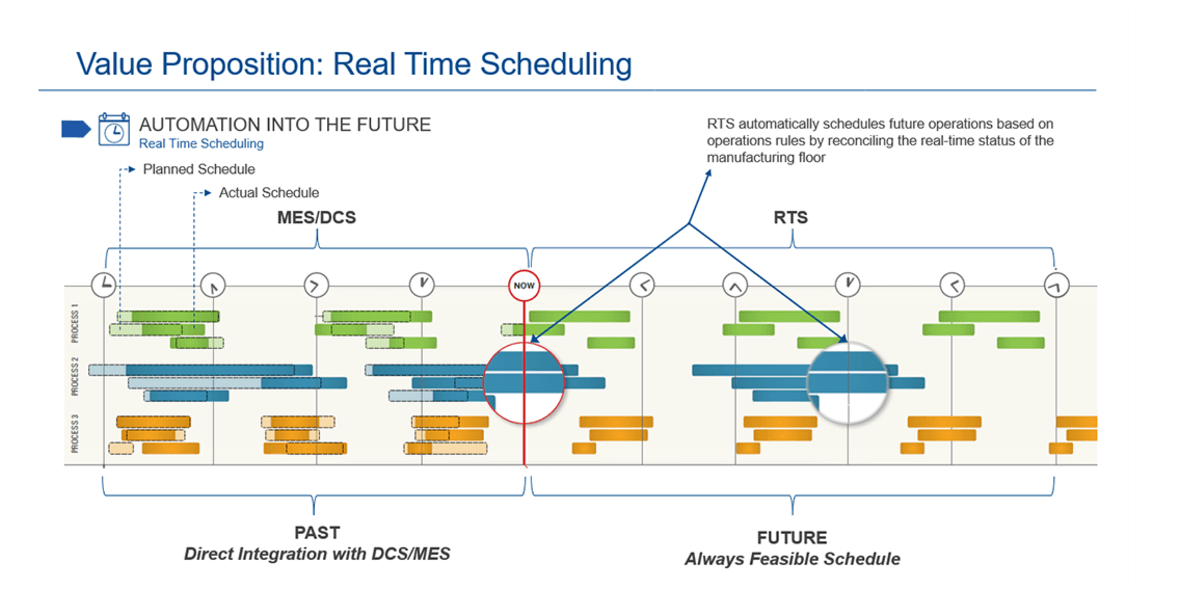
Equipment Monitoring
Much of the room and equipment data needed to ensure proper production performance is not available in an easy to access electronic format. Maintenance technicians and operators perform “rounds” to monitor how the equipment is performing and manually record the results in equipment logbooks, with many of the logbooks still being paper based. Converting that information into actionable data for the plant maintenance staff takes considerable time and effort to transfer it into the maintenance management systems.
The AMS TREX Device Communicator simplifies this electronically captured operator round information and then transfers/links it to an asset management system, such as the AMS Device Manager software. TREX will capture the data and ensure it has the proper context. It can also link to other Emerson asset monitoring systems so that the data collected can be incorporated into an asset management process. The maintenance team can then focus on problem areas with a much broader visibility to relevant information to help keep all key equipment operating on spec.
Rotating Equipment
Most rotating equipment are parts of key production units. If rotating equipment on a critical unit operation suddenly fails, that can cause production disruptions and potential loss of product.
Vibration monitoring sensors, with wireless connectivity options, asset monitoring edge devices, Asset Management Machinery Health Monitoring and Machine Works software provide comprehensive solution to avoid critical rotating failures. Vibration monitors provide real-time insight into the inner workings of the equipment. Other equipment health measurements (e.g., temperature, shaft balance, etc.) can also be monitored and input to the Machinery Health Monitoring software where equipment performance can be tracked in real-time for potential issues, and then diagnosed and analyzed remotely to help avoid production performance problems. Your maintenance team can then focus on problem areas vs just following preventive maintenance standard practices to keep all your key rotating equipment operating on spec.
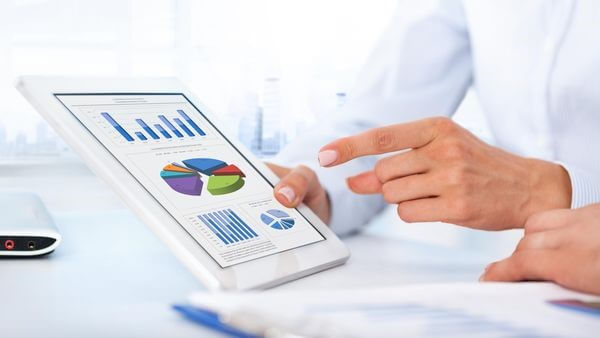
Predictive Maintenance
And finally, the Plantweb Optics platform with the Plantweb Optics Analytics software collects and interprets operational data and information scattered across the plants. This eliminates the need for gathering, analyzing, and reasoning over data and information from control systems, databases, plant applications, and operation procedures. By using artificial intelligence and machine learning techniques, Plantweb Optics Analytics can detect abnormal behavior in the process and with assets in real time and predict future performance. This shortens the decision-making process, preventing further performance deviation and safety issues while maximizing plant efficiency.
Visit the links highlighted above for more on these technologies and solutions to help avoid unplanned downtime and drive business performance improvements.